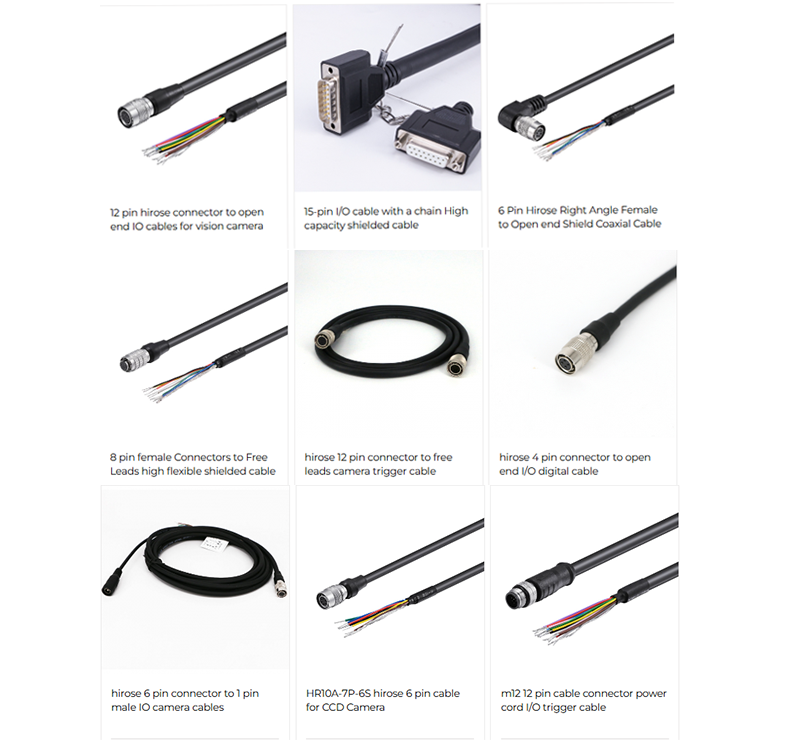
Machine vision cables are important components used to connect various components and transmit signals in machine vision systems. They have the following characteristics and related information:
1. Transmission performance:
• High-speed data transmission: Machine vision systems usually need to quickly transmit high-resolution image data and related control signals, so machine vision cables must have high-speed data transmission capabilities. For example, in some high-speed industrial camera application scenarios, cables are required to support Gigabit or even 10 Gigabit Ethernet data transmission rates to ensure real-time transmission and processing of images.
• Low latency: For machine vision applications with high real-time requirements, the latency of the cable should be as low as possible to ensure that the system can quickly analyze and process the collected images and make corresponding decisions and controls in a timely manner.
2. Anti-interference performance:
• Electromagnetic interference resistance: In complex electromagnetic environments such as industrial environments, there are various electromagnetic signal interferences. Machine vision cables need to have good anti-electromagnetic interference performance to ensure that the transmitted signals are not affected by external electromagnetic signals. Shielding structures, such as metal braided mesh shielding or aluminum foil shielding, are usually used to reduce the impact of external electromagnetic interference on the signal.
• Signal crosstalk resistance: Signal crosstalk may also occur between multiple wires inside the cable, affecting the transmission quality of the signal. Therefore, measures need to be taken to reduce signal crosstalk during the design and manufacturing process of machine vision cables, such as using twisted pair structure and optimizing the arrangement of wires.
3. Durability:
• Mechanical strength: In some application scenarios, machine vision cables may be subjected to mechanical stress such as pulling, bending, and extrusion. Therefore, the cable needs to have sufficient mechanical strength to ensure that it will not be easily damaged during use. For example, some highly flexible machine vision cables can meet the application requirements of frequent bending and movement.
• Abrasion resistance: If the cable is often in contact or friction with other objects, it needs to have good abrasion resistance to prevent the cable sheath from being worn and causing the internal wires to be exposed, affecting signal transmission and safety of use.
• Corrosion resistance: In some special environments, such as the presence of chemicals, moisture, etc., the cable needs to have good corrosion resistance to ensure its normal use and life.
4. Interface type:
• Common interface: Machine vision cables have a variety of interface types to meet the connection requirements of different devices. Common interfaces include RJ45 and M12. RJ45 interfaces are often used for Ethernet connections, and have the advantages of strong versatility and convenient connection; M12 interfaces are waterproof, dustproof, and vibration-resistant, and are suitable for some harsh industrial environments.
• Customized interfaces: According to the specific machine vision system requirements, there may also be some customized interface types, which usually need to be designed and produced in cooperation with equipment manufacturers to ensure that the cable and the equipment are perfectly matched.
5. Application areas:
• Industrial automation: On industrial production lines, machine vision cables are used to connect industrial cameras, light sources, image acquisition cards and other equipment to achieve product appearance inspection, dimension measurement, defect recognition and other functions, which helps to improve production efficiency and product quality. For example, in industries such as automobile manufacturing, electronic manufacturing, and food packaging, machine vision systems have been widely used.
• Robot vision: When performing tasks, robots need to obtain information about the surrounding environment through visual systems. Machine vision cables are used to connect the robot’s visual sensors and control systems to provide accurate visual signals for the robot, enabling the robot to achieve autonomous navigation, target recognition, grasping and other operations.
• Security monitoring: In the field of security monitoring, machine vision cables are used to connect surveillance cameras and monitoring systems, transmit video signals, and achieve real-time monitoring and recording of the monitored area. With the continuous development of security monitoring technology, higher requirements are also placed on the performance and quality of machine vision cables.